Many people aren’t familiar with gas busbars used in gas cylinder testing equipment. In this article, the blasting test bench company will walk you through everything you need to know about them. As the name suggests, gas busbars are systems designed to boost production efficiency, collect gas sources, and concentrate multiple gas cylinders for a steady supply.
A gas busbar is a system that connects several gas cylinders into groups, then reduces their pressure and transports the gas through a main pipeline to the point of use. It’s commonly used in small and medium-sized gas supply stations. Depending on how the cylinders are switched between left and right groups, it can be manual, semi-automatic (pneumatic), or fully automatic.
Here are the key advantages of using gas busbars in a blasting test bench:
1. Reduces the frequency of bottle changes, saving time and labor costs.
2. Helps maintain consistent high-pressure gas, improving safety.
3. Saves space, allowing for better layout planning.
4. Makes gas operations more convenient and efficient.
Gas busbars are ideal for companies that consume large amounts of gas. The basic principle involves connecting gas cylinders to the busbar’s main line using special tools, then regulating the pressure before delivering it to the application site. These steps include pressure reduction and regulation. Today, they’re widely used in chemical plants, laboratories, and research centers.
The gas busbar system typically consists of two main pipelines, with regulating valves in the center to control the flow on both sides. Each group includes smaller valves and other components. A pressure gauge is located in the middle for monitoring. There's also a pressure-reducing device on top for easier pressure adjustment, along with low-pressure regulators for gas replacement.
Proper use and maintenance of gas busbars are crucial for safety:
1. When opening, slowly turn the shut-off valve before the pressure reducer to avoid sudden pressure surges that could damage the system. Adjust the screw clockwise to set the desired output pressure on the low-pressure gauge. Then open the low-pressure valve to start the gas flow.
2. To stop the gas supply, loosen the pressure reducer completely, wait for the low-pressure gauge to drop to zero, and then close the shut-off valve. Avoid leaving the pressure reducer pressurized for long periods.
3. Safety valves are installed in both the high and low-pressure chambers. They automatically release excess pressure when it exceeds safe limits and reseal once the pressure returns to normal.
4. Ensure all connections are clean before installation to prevent debris from entering the pressure reducer.
5. If there’s a gas leak at the connection points, check if the threads are tight or if the gasket is damaged. Tighten or replace the gasket as needed.
6. If the pressure reducer is damaged, leaking, or the low-pressure gauge keeps rising without returning to zero, repair it immediately.
7. Always use the busbar according to the specified gas type and never mix different gases.
8. Keep oxygen busbars away from grease to prevent fires.
9. Avoid installing gas busbars in areas with corrosive substances.
10. Never inflate cylinders in the reverse direction.
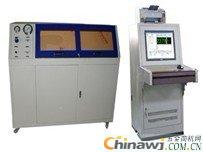
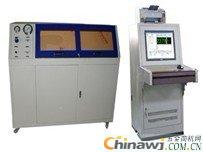
outdoor wall lights,garden lights,festoon lights,outdoor string lights
HSONG LIGHTING CO,. LTD , https://www.hsonglighting.com